BnF Ms Fr 640 p100v RECONSTRUCTION OF IMITATION GEMSTONES
Friday, Oct 16, 2015
making and knowing lab, chandler hall
9:05am
MARJOLIJN HAS PHOTOS
1.5+ hrs spent as a group deciphering problems in the manuscript and its translation. These mostly revolved around understanding a "dram" and "un gros (de sel)". Re: dram, we were not sure if this was meant to equal 3.54g or 1.77g as per Avoirdupois system. We settled on 3.54g after consulting other sources, namely Middle French dictionaries.
8 drams made 1 oz = 8 drams = 28, 34 grams - Cotgrave:https://books.google.com/books?id=ISi4M196tl4C&pg=PT221&lpg=PT221&dq=cotgrave+dram&source=bl&ots=AEqZMFf_sx&sig=FJjgDLl1ELXqeY7yYmAueloCd2I&hl=en&sa=X&ved=0CDYQ6AEwBGoVChMItej73prHyAIVBqkeCh3cBwOj#v=onepage&q=cotgrave%20dram&f=false
Next was the issue of "un gros de sel" written in a marginal note, and how exactly to translate "un gros de". A pinch? A piece? Coarse salt? "Gros sel" appears multiple times in the manuscript but "gros de sel" does not.
We decided on 3 trials with varying additions of alkali salt
- 1:3:1 (quartz powder:red lead:alkali salt)
- 1:3:1/2
- 1:3:2
10:45am
preparing to begin
We are using:
3.5g Kremer 58620 Quartz Powder (in tub,
not coarse one in plastic bag)
10.6g Kremer xxxxx Red Lead (in tub, wrapped in plastic)
3.5g Kremer xxxxx Potash (potassium carbonate, in tub)
BEWARE: red lead is incompatible with aluminium, it can form an explosive compound.A reminder to always look (and re-look) at safety data sheets!SET UP in FUMEHOOD:To prepare for the process of mixing, I first thoroughly wiped down the entire surface/ground of the fume hood with wet paper towels, then wiped it down again with a dry paper towel. We then spread out newspapers across the entire surface, several layers thick (as many sheets as could comfortably slide under the vertical poles at the rear of the fume hood--approx. 2-3 sheets). Next we spread out damp paper towels, particularly in areas where there would be lead. A glass plate was set on top off the wet paper towels and then topped with a wet paper towel to prevent the copper sheet on top of it from sliding around. All the ingredients were placed on the left side of the fume hood interior--in their plastic tubs. Two stainless steel "scoopers" and one plastic spoon (for red lead), the scale with a beaker on top of it (set to weigh in grams).Trial #1I measured out 1 dram (3.5g) of the quartz powder into the beaker. I replaced the lid onto the tub of quartz powder and placed the scoop I had used next to it to make sure I only used it with that one substance. I transferred the powder onto the copper sheet by gently pouring it out--tipping the beaker with its lip touching the sheet and slowly raising the bottom of the beaker up, gently tapping the back to get all of the powder out. I consolidated the powder using two small palette knives. I reached for the muller and placed it on top of the powder to begin grinding and was surprised at how much seemed to blow away because of the way I placed the muller down. I did not force it or move too quickly, but I needed to be even more gentle--the powder is extremely fine. I reconsolidated what had blown away, pulling it forward with the palette knife, and very gently set the muller down on top of it a second time. I did not see any of the powder fly away this time.Grinding was quite challenging to start--I was worried about the powder blowing away and also aware of how much powder was on such a small copper sheet. I would have felt more comfortable if we had had a larger copper sheet, but given the small size of it, it seemed like a lot of the powder could easily be pushed off the sheet and end up on a wet paper towel. I grinded with a lot of force, beginning in a small area and making a 'figure eight' shape as recommended by Marjolijn. Within a few minutes--maybe 2--the process was much easier. It is hard to say whether I simply became familiar with the material I was working with, with the movements, or if it was getting easier because it was being ground down. There was definitely a sound to the grinding, but to hear the sound it required a lot of pausing to reconsolidate the powder and begin grinding a different portion of the amount on the sheet. within 5 minutes, I noticed a color change in the powder; it had gone on the sheet and looked quite white, but as I would scrape bits of it back together with the palette knife, I noticed very clear distinctions between a white powder and a light gray powder. The more I ground, the more the powder turned gray. We also remarked on how much of the color of the copper sheet had changed. While grinding, we were simultaneously polishing the copper, making it seem like the powder must have been absorbing tiny bits of the copper which, we had suspected, would assist in turning the finished "gemstone" green. Marjolijn also suggested that it might be turning gray due to residual oil still on the muller. It would be good to make sure the muller is as clean, oil-free, and dry as possible.
We (Jenny, Marjolijn and I) took turns grinding the powder to get a feel for it. We felt it had been thoroughly ground when all of the powder had turned dark gray--I had taken my watch off but would estimate 10 minutes. Then, before incorporating the red lead, we followed safety instructions to prepare for working with it. Dust masks, goggles, and double layers of gloves, tapped around the wrists (this was not done so properly to start but I was retaped by Pamela shortly after). The safety person who was present asked if we could begin with a smaller dose of lead than was called for, as an addtional safety precaution because he said there might be some kind of reaction. We agreed to start with one dram (instead of three) to see if anything would happen. I lowered the fume hood slightly for extra precaution and opened the jar of red lead. With the plastic spoon, I began putting the red lead into the beaker. I was immediately struck by how much heavier the lead was than the quartz powder. I did not feel this in my hand because the spoon only had a small amount...but the scale was showing an increasing weight so much more quickly than it was with the quartz. There was a drastic difference in the weight of the two. 1 dram (3.5g ) was measured out. I closed the lid of the red lead jar and placed the spoon next to it. I gently put the red lead onto the quartz powder and combined the two with two palette knives. I began grinding it. It was very difficult to grind. It was hard for the muller to even move--it felt so sticky or gummy. I mentioned this to Pamela who was standing next to me and she said that the author of the manuscript uses words like fatty or greasy to describe lead. It not only looked like the color of cheetos cheese powder, but it felt like how I'd imagine grinding that would be...it's a powder but it's greasy and sticky. When you get the powder on your hands you can't really rub it off. It spreads like grease. So "grinding" this mixture didn't feel like grinding. There was little sound of grinding as compared to the quartz powder. But we continued. marjolijn and I were the only ones properly dressed/protected to do it, so we took a few turns and then she handed it off to me as she wanted to take photos. This continued and got slightly easier as time went by. I kept grinding and noticed a difference in color--the brightness of the red lead had gotten duller, grayer, as well. The grinding lasted approx 10 minutes.
When it was time to add the potash there was some discussion about whether it was necessary or not to grind it. Pamela and Marjolijn suggested that it wasn't really necessary. The manuscript says to add the alkali salt to a bronze cauldron and then grind. It seems that those with more experience in science or in glassmaking felt it didn't really matter whether it was ground or not. Pamela asked me what I wanted to do and I said I'd like to grind it...or at least crush the potash as they were in little balls. I definitely trusted that they knew what they were talking about (that it's not really necessary to grind) but I thought, since it says to do so in the manuscript, I might as well try to stay as close to it as possible.
I measured out 1 dram of potassium carbonate into the beaker, closed the jar and put its scooper next to it. I swirled the beaker around only briefly, maybe one or two swirls, and it was amazing how it began to turn orange. I had noticed a very tiny amount of red lead left inside the beaker from when I had measured it out (another sign of how "sticky" it is). These few little swishes of the potash seemed to scrub the red lead residue off very well AND take on the color...and from such a miniscule amount of lead. I poured the potash out onto the lead/quartz mixture in 2 doses because there were a lot of these litle balls and I didn't want them to roll off the copper sheet. I simply pressed the muller down on top of each bundle of potash balls and pressed down firmly, just moving my wrist in different directions to break the balls thoroughly under the base of the muller. There was quite a sound--little pops, explosions. It reminded me of both the sound and the sensation of eating pop rocks. Tiny little bursts, quite pleasurable to feel these things crackling under the muller. Once they were popped, I very lightly ground them in with the quartz/lead mixture. I probably would have done this slightly longer than I did but, as others had said it really wasn't necessary to grind the potash, I figured it was equally not so important to get the particles all well blended together.
I consolidated all of the powder/mixture with palette knives. Marjolijn handed me a winder palette knife thing with a rounded tip (sort of like a small spatula) and I used this to transfer the mixture into the crucible. All of the mixture easily fit into the crucible.
It's bright orange. We transferred the mixed powder into a crucible. Then clean up began in order to clear the fume hood for heating up the crucible.
all of the materials that had not had contact with the lead were removed--the jars of quartz powder and potash, their scoopers, etc. Marjolijn and I were the only ones in the protective gear to work with the lead so we worked on cleaning all of this under the fume hood. Everything that had been in contact with lead was cleaned with linseed oil. We cleaned the muller as you would an oil paint brush--she gave me paper towels with little puddles of oil, and I rubbed all over the muller's flat part as well as the body of it in oil. I then rubbed the flat portion on clean paper towels until there was absolutely no red lead smearing across the towel. We thoroughly cleaned the palette knives, etc in a similar way, and these were then washed with soap and water. We gently collected all of the newspapers and wet paper towels that were under the fume hood. It was amazing to see just how far some of the red lead had spread. Its color is so striking, it's quite easy to see small particles against newspaper print. We had to slowly bundle everything up, making efforts to do so carefully so that particles would not drift off the newspaper and onto the surface of the fume hood. When all was properly removed from the fume hood, we removed our gloves and put them in the hazardous waste container, then thoroughly washed our hands, wrists, and upper arms.
Joel then began setting up for the 2nd part of the experiment: heating the crucible.
He used a self-built furnace and I need to talk to him about exactly how he set it up.
There was discussion of whether or not heat the crucible with or without the lid. We referred to the drawing of the furnace on the manuscript page. It looks a bit like underpants (at first...to someone like me who hasn't seen furnace illustrations before) but it also sort of looks like the contraption Joel has set up in the fume hood. The recipe in the manuscript says nothing about placing the lid on it or not so we look atSelf built furnace from Joel set up in fume hood, fire torchsee drawing on fol. 101vwe put the covered crucible into the furnace.we rehearsed what to do in case of emergency, explosion: try first to get torch out of fume hood. close slash of fume hood. leave labwe started as low a flame as possible with our torch in order to not break the crucible.Time12.12 we started to heat the crucible after 1 minute still at room temperature12:13 Joel turns heat up on torch12:14 temperature of the lid raises over 200 celsius12:17 over 300 celsius12:18 over 400 celsius12:23 above 500 celsius our thermometer cannot measure higher temperatures12:30 Joel thinks we now reached about 1500 celsius12:33 joel lifted the lid. its def smolten and fluid, bright red. he can pour itJoel said about 10 minutes of good heatingWe need to go up to about 1500 celsius to reach the melting point of quartz to which alkali salt is addedJ: interesting exeperience when pouring it, it's heavywe observed amazing color changes: bright red in crucible, dark red when poured out, on surface it turned darkish greyish green and it "froze" while pouring. We poured it into a silicon mold and this is where it started to start changing colors very quickly (burned the mold). It was cooling so quickly that a "string" of the liquid started solidifying while it was being poured, forming a thin, slightly undulating needle of glass. It was so hot that it started burning the mold and so we quickly removed it. When we lifted the "glass stone" (with its tail/needle) and rested it on the furnace stone it turned darker and darker and then broke open, showing that it was sort of a very fragile glass bell. it took the impression of our mould very well. Pamela noticed a bubble at the surface and this was the first piece to shatter.it turned darkish blackish green, but the thin glass fiber remained transparent with traces of greenish. when cooling the impression still seemed to change color. turning a little bit lighter green again and slightly goldish.we might have heated it too much as pamela recalls that if it is heated too much it turns black.The color seemed to change slightly for several minutes, even while the glass was cool enough to touch.12:54--inspecting the crucible and it is markedly more green inside than the black stone. As it is pulled out, within moments (less than a minute) the color starts changing. It becomes less green and more black, and then it starts cracking. This seems to be related to how quickly it is cooled. The crucible was kept in the heat chamber and allowed to cool organically, therefore this could be related to why it stayed a greener color than our black glass/stone.
-need to go up to 1100/1200 celsius (to melt copper)
questions:
was it heated to high?
will it require gold to turn red?
color of ruby to green briefly to black--was it cooled too quickly?
-remove crucible lid when stuff inside is molten
Siddhartha V. Shah, Katie Kremnitzer, Joel Klein
Making and Knowing Lab
IMITATION GEMSTONE--EMERALD
11/12/2015
12-2pm
SS:
12:15pm: We have begun to reheat the broken pieces from trial 3 (KK/JK) which is the trial that had the largest amount of copper (0.05g). While the experiment produced a very dark, rich green colored “gem”, the object shattered into numerous pieces and significant crizzling is visible. We are attempting to turn the pieces into a single “gemstone” by cooling it slowly by remelting it, pouring onto a granite slab and placing the hot “brick” on top.
12:21pm: Joel has begun heating all of the pieces from trial 3 on the granite slab with a blowtorch.
12:24pm: heating now on a broken piece of crucible rather than directly on granite and then going to pour onto granite slab
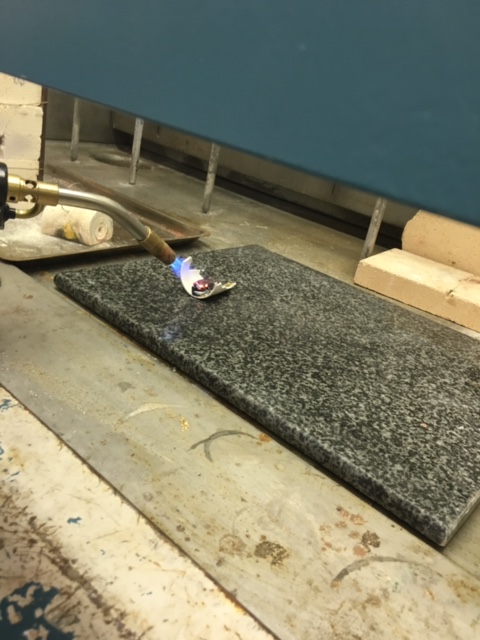
12:25: already quite melted
12:26: under the flame the emerald looks quite black with bubbling on the surface.
12:28: we have stopped heating, entirely poured green mixture onto the granite, Joel placed the brick on top to cool it slowly.
approx 10 minutes later: it has maintained its shape but the surface has a textured and sort of mat finish, likely due to the texture of the brick.
NEW TRIAL:
we are following the proportions used in trial 5 except we have reduced the copper by half. Instead of 0.05g we are using 0.025g. We are maintaining the same amount of salt and we will heat it longer so it is easier to pour, and then we will cool it slowly in hopes that it will not crack. We will do this by covering the poured “emerald” with a crucible.
12:51 Joel is heating, and suggests that we heat for at least 5 mins to get it “really molten”. He is also heating part of the granite slab where he will pour the molten mixture because we do not want the surface of the granite to be too cool and, therefore, to increase the likelihood that the “gem” will crack/shatter
12:54 temp is 805C
12:56 stopped heating
12:57 poured and covered….waiting

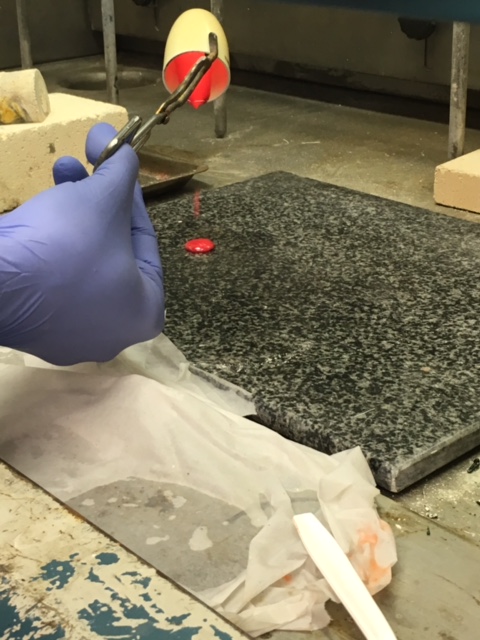
12:59 taking an unmeasured amt of potash and adding it to the used crucible to see if we can “clean” the remnants out
1:01--our trial is a lighter green (perhaps too light to pass as a South American emerald but passing as an Afghani emerald...I am using these descriptives based on recent readings on the colors of emeralds and regional differences as noted particularly in the 16th c) and still quite shiny.
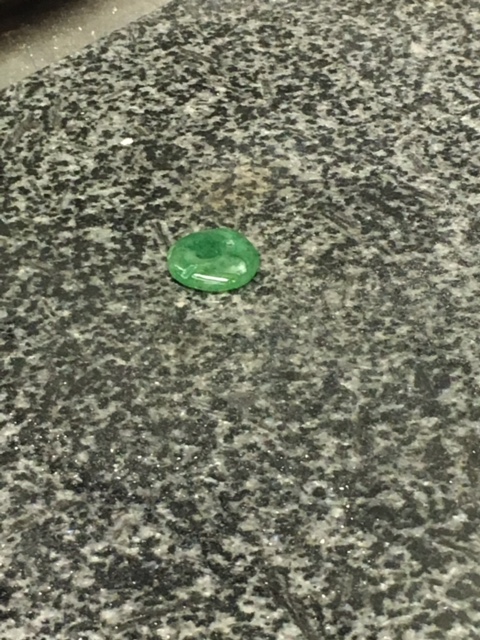
It has not shattered. It has internal fissures that look more like glass than the “veins” and/or imperfections one typically finds in emeralds. The imitation we just produced has a beautiful green color and glossy luster. When held up to the light, however, it seems a bit cloudy inside. Sort of granular or speckled…
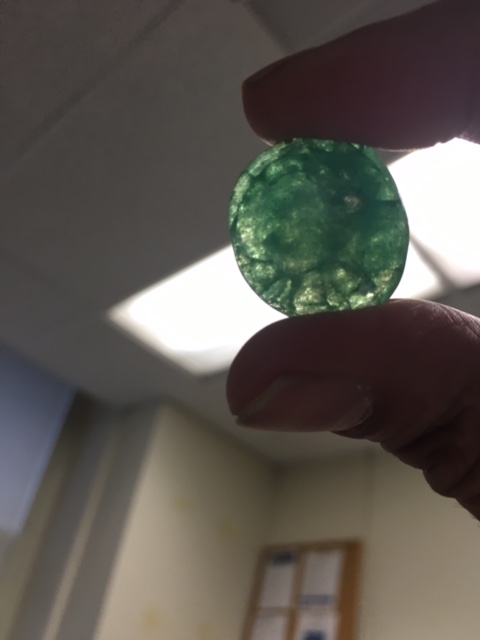
For the next attempt, we are going to grind the potash more finely and stir the mixture while it is molten to see if this reduces the cloudiness of the “gem”.
1:04 pouring remnants
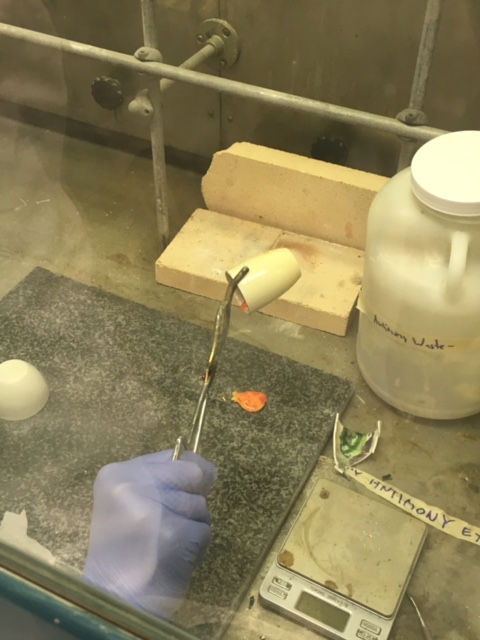
1:08 we are going to redo the experiment now using more copper than the trial we have just completed (trial 6--0.025) but less than trial 3 (0.05)...so we are using 0.038g of copper.
There is some discussion now that perhaps the manuscript author did not actually try this experiment--Joel is discussing how the recipe yields a dark glass, calls for “un gros de sel” which seems to be too large an amount….there is consistent crizzling which seems to be due to the amount of salt used?? This brings us back to our very initial discussion of what “un gros” actually means in the context of this recipe. Katie and I both still believe that it means something like “a pinch”. Furthermore, how do we know that these imitation stones didn’t crizzle when they were made originally? We are wondering whether oiling the “gems” might solve the crizzling issue.**
1:20 all materials added and Joel is going to stir them all “very well”...one minute of stirring using the handle of a plastic spoon.
1:22 Joel is heating and wants to heat for more than 5 minutes this time (a little bit) so that we can stir the mixture more easily and thoroughly
1:26 Joel is stirring mixture in crucible
1:28 it’s been 6 minutes. He is going to get it up to 900 degrees (as last time) and then pour. POURED and covered.
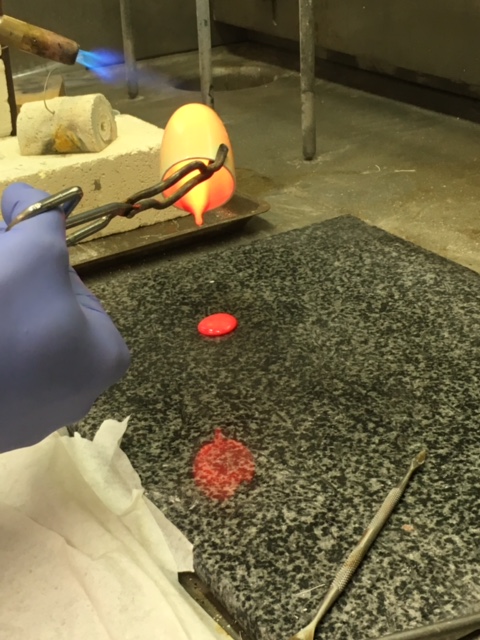
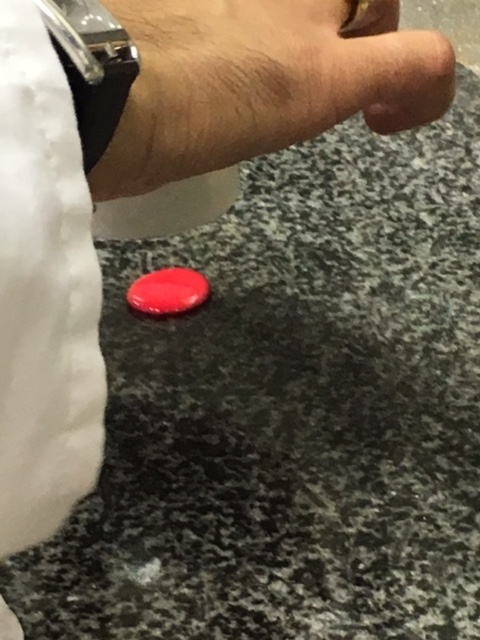
1:29 heating remnants in crucible to 1000.
1:30 done heating
1:31 a few drops of the heated remnants are the color of peridot. Joel thinks this could be because most of the copper poured out in the first pour. This could also explain why the interior of the crucible is so close to yellow
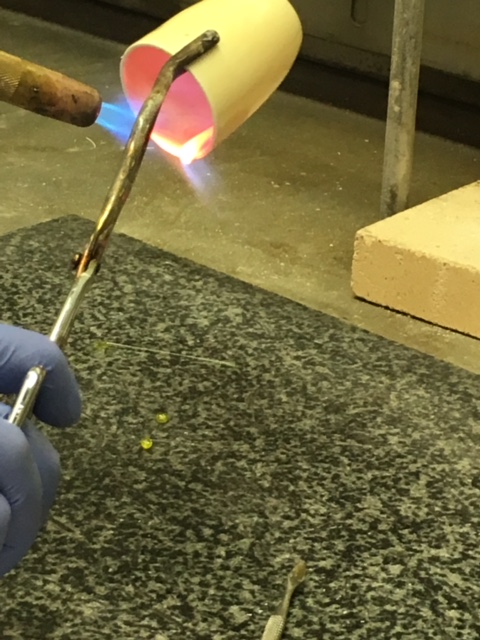
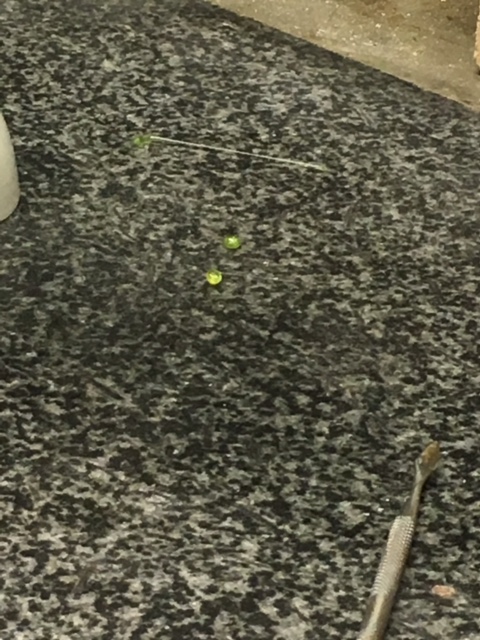
1:42 The result is, in my opinion, the most successful of all our attempts. There is a bubble in it at the top which is just above a slightly stained, rough, mat portion of the bottom which made direct contact with the granite. This could be because of some kind of coating on the granite slab that came off. The color is very close to that of a genuine emerald and the luster is very fine--shiny, smooth, reflective.
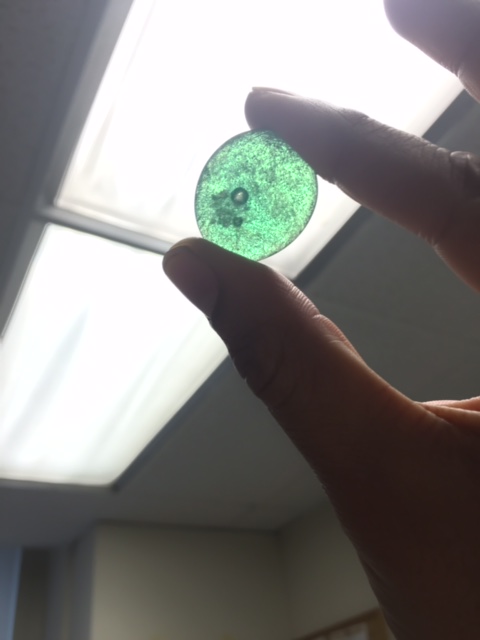
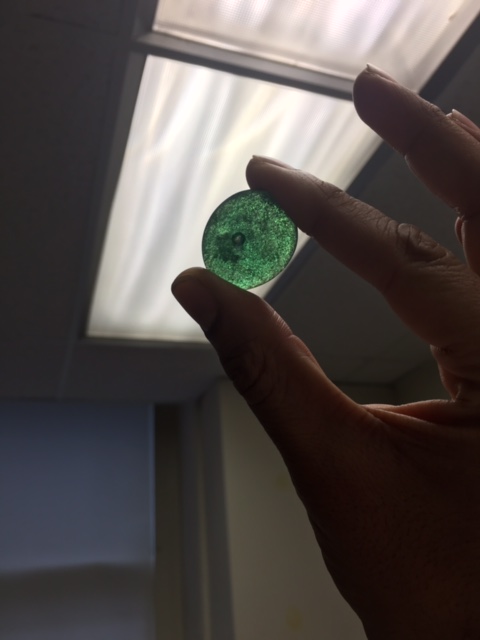
1:52 last trial just cracked in my hands after taking photos of it.
Considerations for next trials:
-we have been using copper powder instead of just grinding on the copper sheet to insure that we have enough copper to make the result green. Now that we have made several attempts with different amounts of copper, it might be interesting to record the amount of time it takes to collect a comparable amount of copper powder by grinding on a copper sheet and collecting the dust
-the small “peridot” beads we produced are quite beautiful and convincing. Perhaps we should try pouring the emeralds in small amounts rather than all in one “medallion”. It would be interesting to see if small drops would look even more convincing than the single medallions we have been attempting to produce