GESSO ON WOOD PANEL experiment
Tuesday, October 6, 2015
Making and Knowing lab, Chandler Hall
10am
After quickly (approx. 3 minutes) sanding down the front side of the 16" x 20" wood panel, I applied water to the back of the panel in horizontal strokes. The front is only lightly sanded--it appears more of a dusty brown than when first removed from the packaging and light marks are visible on the sanded side from where I used the sand paper. Most of the sanding was done in a rapid, circular motion.
10:08am
1st layer of gesso applied to the front of the sanded wood panel by Marjolijn as an example of how to do it for the class. The gesso looks to be the consistency of house paint, perhaps a bit wetter but I have not yet worked with it myself.
10:40am
The 1st layer of gesso is dried. It is dry to the touch but also visibly dry--no darker, wet patches on the surface. Sanding with thickest grade of sand paper, in circular motions, rapidly.
10:44am
Sanding completed. Water applied to the back of the panel in vertical strokes (I am wetting and painting gesso on in same direction). Applying gesso in VERTICAL strokes
10:50am
2nd layer of gesso application completed. It's quite difficult to cover the surface as smoothly as Marjolijn demonstrated. She has a skill and ease at doing this that I don't--perhaps because she has, I'm assuming, done this many times before or perhaps because she has a background in painting? She is able to wet the brush with gesso, and pull it across the panel in a very even, solid brushstroke--she puts the brush to the panel and makes a smooth line all the way across. I can't seem to get the gesso to move so smoothly. If I put on too much it looks drippy and I have to spread it around...my strokes look more painterly. Assuming I can just keep sanding, though, to get rid of the ridges that occur from too much gesso in particular areas.
11:28am
2nd layer is dry. Sanding.
11:30am
Done sanding. Brushing water onto the back in horizontal strokes. Noticing I'm not being particularly mindful about how I put the water on. I still don't fully understand how it helps the panel from buckling (scientifically, I mean, I don't understand how it works) but I gather it doesn't matter so much how even the strokes are or how much is on the back. As long as it's wetted.
11:32am
3rd layer of gesso in horizontal strokes. This 3rd layer feels more difficult than the 2nd, but I think that's because one brush-load of gesso has to cover a horizontal length rather than vertical--there's more distance to cover in a single stroke. Still trying to get the gesso to get across the panel in a single stroke but haven't figured out exactly how much gesso to put on the brush and how much pressure to apply with the hand. I am lightly dipping the brush in the gesso and then tapping it against the side of the glass jar that contains the gesso before applying it to panel. I'm doing this because I saw Marjolijn doing this, presumably to make sure there's not too much gesso on the brush which would then increase drying time and likely lead to more uneven surface.
11:37am
3rd application completed. Drying.
12:43pm
3rd application is dry. It seems to have taken longer than previously. I was told this would happen--that, the more applications of gesso are made to the panel, the longer the drying time would be. So noticing that now with this layer. Sanding with thickest grade sand paper (STILL), mostly circular motions but also some vertical and horizontal "scrubbing", particularly around areas where there are ridges caused by areas where gesso was applied more thickly. I can still see the brown of the board beneath the layers of gesso but I think it should be gone with the next layer or so.
12:54pm
Wetted the back of the panel and applied 4th layer of gesso in vertical strokes. This time it was easier than previous layers. Again, possibly because the vertical strokes are shorter and so the gesso tends to make it across the surface more uniformly. Also it feels smoother when I apply the gesso to the surface--the gesso glides across more easily. Perhaps I am also getting more used to the kind of motions necessary to apply it evenly.
1:50pm
4th layer of gesso is dry. Sanding. There is more and more dust coming off the board so I am now wearing a mask. It's quite exhausting to the arms to sand and frustrating that my left hand is so much stronger than the right. Also the motion of sanding comes more naturally with my left hand than my right hand--I can't seem to hold the paper quite so firmly with my right hand, or move in such uniform ways as with my left. Still doing mostly circular motions but also vertical and horizontal "scrubbing". Quite a bit of dust comes off now with each sanding session.
1:57pm
5th layer of gesso being applied to board in horizontal strokes...also wetted back before doing this. The brown surface of the wood board is now invisible, covered in the off-white color of the gesso. This was the fastest and easiest application of gesso horizontally so far.
2:56pm
5th layer dried. Sanding with thickest grade sand paper. Quickly, aggressively, circular motions across "body" of panel and in scrubbing motions around the edges where the gesso is building up and a bit lumpy.
3pm
Finished sanding and applied water on the back. Then gesso in vertical stripes across the panel (front). Quite easy, smooth, I may have applied a bit too much on this layer but it is my last layer for the day and I can sand more aggressively tomorrow to try to get a more even surface.
3:05pm
6th layer applied and panel is drying until tomorrow.
Wednesday, October 7, 2015
Making and Knowing lab, Chandler Hall
10:10am
Sanding dried panel to prepare it for 7th layer of gesso
10:26am
I sanded for approximately 15 minutes just now. As I approach the final (8 or maybe 9) layers, I am starting to see the increasing importance of sanding the surface down to get as close to a smooth even surface as possible. Still not sure how my panel will look anything like Marjolijn's "test board" panel but trying! I sanded with the toughest grade of sandpaper for 10 minutes and then switched to the finer paper...I used the toughest paper particularly on thicker parts of the panel where the thick, dried gesso needed to be brought down--rubbing the finger across it, one would feel the lump of ridge of it. I thoroughly sanded these tough areas and then switched to the finer sandpaper for the entire surface. I notice how the finer sandpaper is starting to give the panel a glossier or more polished looking surface. Wetted the back and applied gesso in horizontal strokes. Easier to apply, the gesso is "fresh", as in it has just been prepared so it is of a very light, thin consistency which makes it easy to work with. Not lumpy or dried or pasty in any way. I'm getting more and more particular about my panel as I approach the final layers. I want a smooth, even surface.
11:37am
7th layer of gesso is dried. Sanding.
12:16pm
I sanded for 8 minutes. 5 minutes with roughest paper and 3 with finer paper. The 7th layer was quite successful and didn't seem to need much sanding. The gesso dried rather evenly across the surface, just a few areas that needed extra attention with the sandpaper.
12:20pm
applying 8th layer of gesso vertically across the panel. I am certain I will need a 9th layer...It feels like a "feeling" that I need one more layer. How do I know this? Hmmm...One more coat will, I am guessing, go on very smoothly and evenly. I have enough time today to apply one more after this 8th layer, and then to let it dry over night before doing a very vigorous sanding tomorrow. So since i have the time, I will do a 9th layer. It won't hurt.
12:26pm
8th layer applied. It went on smoothly, there are some "chunks" in it so I am glad I will apply another layer--not sure what these chunks are. Maybe dried pieces of gesso from the paintbrush I just used? Dust in the room?
1:30pm
8th layer is dried. Will do a rigorous sanding before applying 9th and final layer of gesso.
2:10pm
I sanded the panel for 40 minutes, beginning with the roughest sandpaper and finishing with the finer sandpaper. I tried to use the finest sandpaper we have but I it seemed pointless since one more layer of gesso will be applied. applying 9th layer horizontally across panel. Easiest layer to apply so far. The gesso went on smoothly in each stroke, the surface is covered and it doesn't look like too much was applied. letting it dry now and will check on it tomorrow when I return for final sanding and application of isolation layer.
Thursday, October 8, 2015
Making and Knowing lab, Chandler Hall
12:58pm
Arrived to sand down final layer. I was looking for my board and had a hard time locating it. When I found it, I realized I had passed it up assuming the one that was mine absolutely could not be the one I had worked on yesterday. I was looking for a more-or-less finished, clean board. My board looked very strange. There were unusual little spots on it--presumably air bubbles? The surface did not look uniformly covered as I had assumed it would be. When I applied the final gesso layer yesterday, I felt quite confident about how well it had gone on. Seeing the board today, I see that it dried far less cleanly and smoothly as I had imagined. I will sand with the three different kinds of sandpaper, going from thickest to thinnest. Marjolijn recommends sanding for about one hour.
2:10pm
I've finished sanding and it looks to be ready for the final layer. I sanded for over an hour, working up quite a sweat. the finer grain sandpapers are used up within a matter of minutes. I must have through 4 sheets of the 800 and 1000 grade/grain sandpaper. I showed the board to Marjolijn and she said it looked ready, but then suggested we try Cennino Cennini's method of testing whether or not the board is ready.
from
The Craftsman's Handbook, p. 74
"HOW YOU SHOULD START TO SCRAPE DOWN AN ANONA FLAT GESSOED WITH GESSO SOTTILE, CHAPTER CXX
When you have finished gessoing, which must be finished in one day (and, if necessary, put in part of the night at it, just so you allow your required intervals), let it dry eithout sun for at least two days and two nights: the longer you let it dry, the better it is. Take a rag and some ground-up charcoal, done up like a little ball, and dust over the gesso of this ancona. Then with a bunch of hen or goose feathers sweet and spread out this black powder over the gesso. This is because the flat cannot be scraped down too perfectly; and, since the tool with which you scrape gesso has a straight edge, wherever you take any off it will be as white as milk. Then you will see clearly where it is still necessary to scrape down."
For this, Joel ground up charcoal and placed it in a few layers of cheesecloth, wrapped up to make a kind of pouch. I then gently patted the pouch across the gesso'd board, quick gentle pats across the surface, uniformly...it was a bit like using an old, large powder puff. Once the surface was covered in charcoal dust, I took goose feathers and swept across the surface of the board, first spreading the dust across the surface evenly and then using the feathers to sweep the dust off the panel. The more I swept off, the whiter the surface got (returning to the color it was before applying the charcoal), but there were lots of marks all across the surface. Areas that had been overly sanded with the most abrasive sandpaper became visible--scratches, filled in with charcoal dust. There were many spots of charcoal as well, evidently air bubbles or patches that had simply not been sanded down thoroughly. Most of the central part of the panel was very clean and smooth. The extremities of the board were the areas with the most issues--not uniformly sanded, sanded down but not properly smoothed out using the finer sandpaper, these pores or bubbles that needed to be sanded down. I thought I was done but this test revealed to me areas that needed more work. For the final sanding, I will just use the two finer kinds of sandpaper.
3:40pm
I spent another 35 minutes sanding the board until it was very even, smooth, and uniform. I addressed the problem areas and they are all quite smoothed out. Then Marjolijn and I worked on producing the isolation layer using a 1:15 ratio of rabbit glue and water. We let this "cook", and when the dry particles had thoroughly melted, the glue was ready. I could not find a ruler or measuring tape so I estimated what looked like the middle of the board and applied a piece of tape there to separate the board in half--one half will have the quadrants on it and the other will be left plain for now. I then applied a the isolation layer very thinly to the area that will be separated into little squares. There were some glue chunks that got on the surface but I tried quickly to remove these. The glue is very watery and I was not able to get it on as evenly as I would have liked. I am expecting some dried drips on the surface but I will see how it is on Monday.
Monday October 12, 2015
Making and Knowing Lab, Chandler Hall
9:40am
I arrived at the lab at 9:05am this morning. Not so happy with how the glue dried--I had seen one area in particular that had a big drip on it before leaving last week. Seeing it dry, it's quite an unusual darkish spot. By "darkish" I would say it is a pale, khaki or sandy color. A blob that is perhaps 3inches wide at its widest part and 4 inches tall at its tallest part. Furthermore, there are areas along the edge where there are dark pock marks or spots that look like the holes that had emerged when I had tapped the gesso'd area with charcoal. Marjolijn looked at the board and suggested I take photos of the glue blob as hers did not have the same reaction--we both used the same pot of isolation layer on the same day. Perhaps I simply had too much on my brush when I applied it to that particular area where there is a darkish mark. Re: the dark spots, she suspects that perhaps I sanded too hard because it looks like I went almost to the original wooden surface of the board! I's interesting to feel the difference in the texture of the gesso'd half of the board and the one with the isolation layer. The gesso half is smooth, milky, almost glossy. It's very uniform and seems just right. The other half is rough to the touch, almost like sand paper.
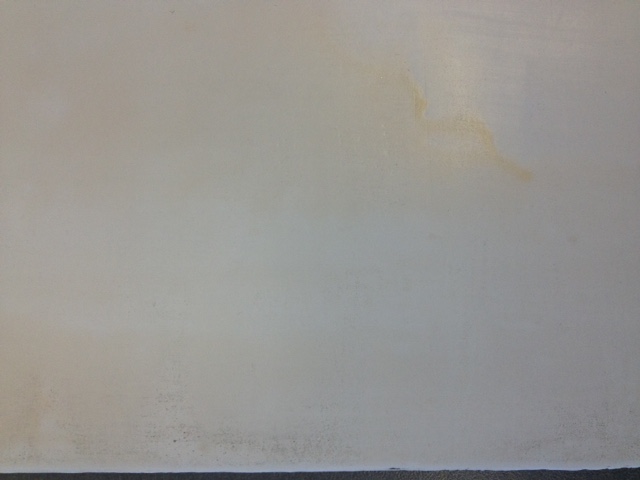 |
half the panel has isolation layer on it with stain visible on this portion of panel |
Without a ruler or measuring tape in sight, I have just estimated box sizes. I cut pieces of masking tape in half lengthwise which was not so easy and clean. My squares for the testing half of the board are not uniform and not very neat BUT I do not think this will make much of a difference as these squares are meant for experimentation. I have labeled the boxes by #/Letter (1A, 1B...2A, 2B, etc.). The board goes from 1A to 8F (48 squares).
10:20am
Watched Marjolijn make a paste out of German bole--adding water to a pile and grinding it with the glass thing (muddler? What's it called?). It did not take too long for it to be a paste to which she added the 1:15 solution from the isolation layer. Applied three coats to 1A (writing this at 6:54pm...just home after being in lab all day and did not take notes while there so this is a summary). The first coat dried very quickly--I would say within 10 minutes. We only did 3 coats and the final coat took nearly an hour to dry. My brushstrokes were quite thick...again.
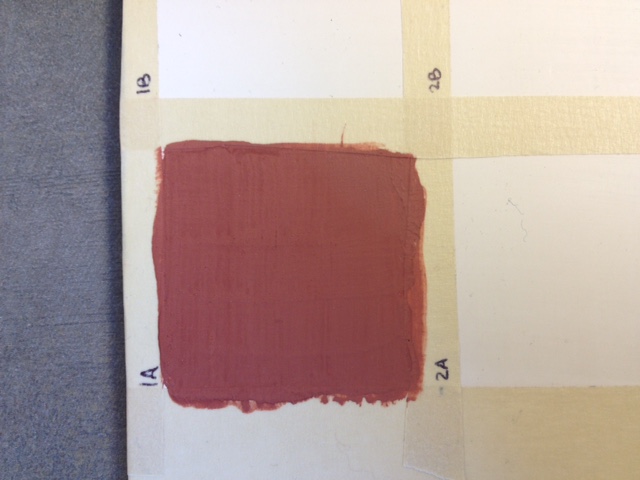
The next step was to rub in over and over with a piece of cloth--I cut myself some cheesecloth, bunched it up, and began working the surface. Marjolijn suggested I do an ahistorical method and use 1000 grade sandpaper to work the surface as my square had thick bits of the bole mixture on it and the intention is to get it nice, flat, and shiny. I wouldn't get there with the cheesecloth alone. I sanded it down for approx 10-15 minutes and then rubbed it with cheese cloth for another 15 minutes or so.
around 2pm
I began to use the burnisher to further polish 1A. Also made a solution to later be applied to 1A once it was ready for gilding--5ml everclear, 20ml water, and she (Marjolijn) added the 1:15 RSG solution. Instructions said "a drop" but she clearly added more than that. I asked her how one of us would know how much to ask without having done it before--she said, "you probably wouldn't". In appearance, the final solution was slightly cloudy. Both the alcohol and water are very clear--there was enough RSG mix added to this solution to make it visibly cloudy but not anywhere near white or milky in appearance.
Polished 1A for a good 30 minutes at least with the burnisher until it was ready to be gilded.
3:30pm
Marjolijn and I are beginning the process of gilding. She is helping me because it seems to be a very complicated, sensitive process that requires a good deal of experience. She gets out her supplies which include: gold leaf, suede "pillow," gilding knife, thin brushy device for picking up and placing gold, burnisher, very fine brush. It moves as if it is alive, that was the first thing that came to mind. It is so sensitive to air, wind, breath, etc. When she picks up the sheet, it flickers and appears to move from here to there according to its own fancy. This is because it is so light.
She begins by cutting the gold leaf into a small size to approximately fill 1A on my board.
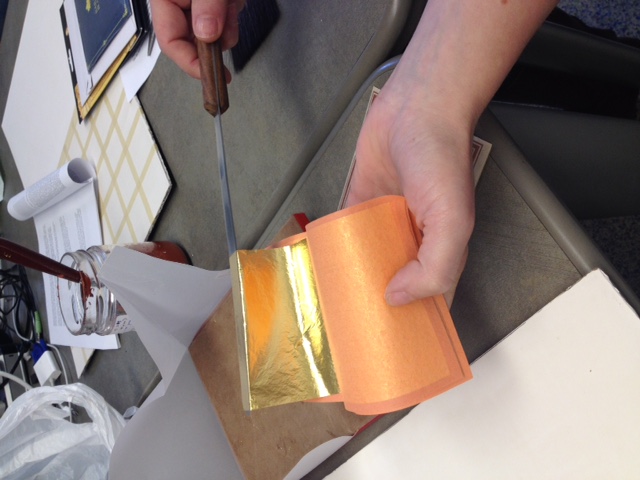
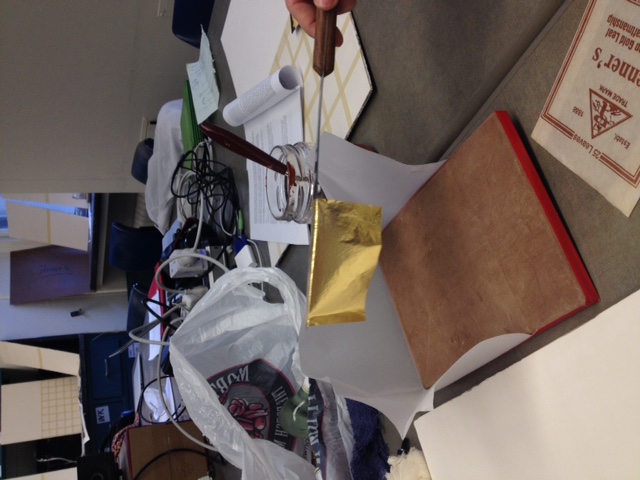
When she had finally cut the gold leaf to approximately the right size and was able to pick it up with the brush I quickly applied the adhesive coating to the square. It was quite difficult to pick up. She rubbed it behind her ear and on her wrist to get a static charge but it was not working. I recommended my greasy t-zone and it worked. I had to reapply the glue mix three times because I would apply it but she was not able to grab the gold...and the adhesive mixture dried within seconds. You could see it dry so quickly. Where there were uncovered patches, we added extra bits of gold leaf to fill them in. Errors were filled in. An effort was made not to get any of the glue solution onto the gold leaf as it would discolor the leaf. This photo reveals a small area that was repaired--there was a hole that we filled in with a tiny piece of gold leaf. Apparently a tiny bit of the adhesive solution got onto the gold as you can see a spot with a different color on it.
Over the next two hours we tapped it with the burnisher as Marjolijn said there is a sound it should make when it is properly dry. Over and over, we heard the sound (where it sounds almost like the board without anything on it...meaning, when you first apply the leaf and tap that portion with the burnisher, it has a low and muffled sound. It is done when the tapping of the leafed area sounds very close to tapping on other parts of the board) but it was not ready--she or I would try polishing the surface with the burnisher, and it would start to break the leaf, at which point we would fill in the torn part by reapplying a tiny amount of the RSG mixture and putting on a piece of the gold leaf. At 5:30, we had tried again and torn another portion of the leaf so, filling in the space with gold leaf, I left it to dry. Our guess is that the conditions of the lab are somehow not letting the leaf dry correctly. It's curious--Cennino Cennini mentions in his book that application of gold leaf should be done on a damp day, presumably because the humidity assists in the binding process? I'm confused by this--how would a humid environment encourage something to dry?
Another question I have, given the amount of time this is taking...if gilding was best done on humid, damp days, might there have been a schedule for doing this in workshops? If a number of paintings were commissioned, would gilding be done during certain months or seasons and avoided in other months/seasons...during which more painting would be done?
Thursday Oct 15, 2015
making and knowing lab
12:35pm
horizontal black line through each of the following squares
2A: standard linseed oil/copper green/Kremer-73054 Linseed Oil, cold-pressed w/ mucilage deposits
2B: "sun-thickened"
2C
2D