Stucco for Moulding Reconstruction
Day by Day Entries
NAME: Jef Palframan
DATE AND TIME: 171600 Sep 14
LOCATION: Brooklyn, NY - Apartment on 20th floor
SUBJECT: p0029r - Stucco for Molding Reconstruction (SMR)
- Before we attempted our second iteration of the BMR we had intended to use tragacanth gum in one of the mixtures. Upon closer inspection of the recipe it became clear that the 'stucco' was intended as a sculpting agent and not for casting. Obviously this did not fit into the BMR experiment. For the sake of curiosity, and partially because I had already bought the tragacanth gum (which was rather expensive), I decided to attempt the recipe on my own.
- Equipment:
- Stucco knife - tragacanth gum when in a jelly form is extremely difficult to work with. In order to manipulate the material it was necessary to grab a modern stucco knife. As is described later in these field notes the tragacanth gum presented a high level of agency (See. Ingold ch. 18 and Lehmann).
- Granite Counter Top - It was necessary to use a modern polished marble counter top. The experiment started with a wooden cutting board, however it was necessary switch as the adhesion of the tragacanth gum was too much.
- Ceramic Mixing bowl - No anticipated effect on authenticity.
- Stainless Steel Mixing bowl X2 - No anticipated effect on authenticity.
- Plastic measuring spoons - No anticipated effect on authenticity.
- Silicon Mixing Spatula - No anticipated effect on authenticity.
- Crome Mixing Knife - used in painting. No anticipated effect on authenticity.
- Ingredients:
- Tragacanth gum - the only tragacanth gum that I was able to obtain was in a finely powdered form. The recipe called for the tragacanth gum to be "dip[ed] into; to drinks all the water and is swollen and turned into jelly". This may indicate that it could be in a purely solid form, as 'dipping' implies a solid object.
- Rye flour - Rye flour was selected as the recipe states that it is better than wheat.
- Linseed Oil - The recipe calls for cane oil, AKA calamus oil derived from the Acorus calamus root, however cane oil is toxic and is banned in the US (See http://www.accessdata.fda.gov/scripts/cdrh/cfdocs/cfcfr/CFRSearch.cfm?fr=189.110). I decided to substitute linseed oil, due to its drying properties when used in painting and my past experience with it. I did not add any turpentine as I would usually do while using it as a painting medium.
- Serial #1:
- The recipe states "Have some tragacanth gum and let it dip until it drinks all the water and is swollen and turned into jelly. Then grind it strongly on marble..." (p029r). I am taking this to mean that the gum is in a solid state as opposed to the highly refined and powdered form than I have. Since we are instructed to 'grind [the jelly]', I may achieve the desired result if I produce a malleable homogeneous substance.
- I commenced filming and combined tragacanth gum in a plastic mixing bowl with water. I placed 1 Tsp of tragacanth gum in a bowl and added about a table spoon of water. This immediately disappeared into the powder forming hard blobs that later resisted dissolving. I added more water in attempt to break up the clumps and this was my first learning experience. The tragacanth gum reacts very strongly with water; it absorbs the liquid very quickly and even a slight dusting of the gum in powdered form sticks to any moisture and forms a rather disproportionately larger slick oily layer that is very difficult to wash off. Once it absorbs a small amount of water it can harden very fast and prevent further dissolving even when immersed in water. I continued to add water, one Tsp at a time, until a "jelly" (as p029r calls for) starts to form. In order to achieve the desired consistency I have to remove it from the mixing vessel and start to grind it on the marble counter top with a stainless steel stucco knife. While this might have affected the authenticity of the experiment, it was necessary. The gum is just to difficult to manipulate with porous materials like wood and hands. Smooth materials are required.
- After 20 mins of mixing I added linseed oil with a brush as stated in the recipe. With the addition of the oil the mixture became much more manageable. I was concerned at first because the material seemed to separate uncontrollably, however after applying more pressure and mixing for another 10 mins the cohesion was regained. Because of the oil the material was much more manageable with bare hands and could be manipulated into three dimensional objects as the recipe suggests.
- After arriving as the end of the preparation phase, I had to decide what to sculpt. If occurred to me that this is a step that should have been performed before the experiment started. The object that I would have intended to sculpt would have had placed demands on the material I was mixing to build said object. The final material could be molded into a two dimensional figures placed on a flat surface. I ended up crafting an antler (or a branch, I really am not a sculptor) (on left in picture below).
- Serial #2:
- In the second serial my goal was to increase the strength of the material and the detail it could handle. I also wanted to create a large batch in order to see if I could sculpt a larger object.
- To start this iteration, tried to mix the tragacanth gum in a way that it would not clump and be difficult to work with. I tried to drop the gum into water a bit by bit, but it would not dissolve. I ended up mixing it in the water and experiencing the same problems as before. I ended up mixing 1 ΒΌ cup of water with 3 Tsp of tragacanth gum.
- Adding the flour little by little to the tragacanth gum proved a difficult way to judge the appropriate amount with such a large amount. In total, I added 1 Cup of rye flour.
- When it came time to add the linseed oil it was difficult to judge how much should be added. The recipe says to "rub it with some cane oil with a brush so the oil soak into it to make it more detachable" (p029r). Since I was working with a much larger amount as the last time I added more oil to the mixture. However, I did not experience the same separation of the material as I did the last time. Even with the addition of the oil the mixture remained very sticky. The mixture became more viscous and remained sticky and difficult to work with the more oil I added. I eventually go to a point where I felt that I have had too much oil and the added some additional flour to counter act the wetness of the mixture.
- In the end the mixture came out very different from the first iteration. This mixture was much harder to work with even with the addition of the linseed oil, it stuck to hands and even the . It was much weaker and was not as easily manipulated as before.
- I decided to try sculpting it into a "bed ornament" as the recipe calls for. I was (sort of) able to craft something that looked like an ornament (pictured on bottom in picture). This was more due to my sculpting skill, not the material.
- Within a day both results were dry. The models had become extremely hard and sturdy. The 'stucco' proved to be an amazingly strong material.
- After a few days some cracks in the second model appeared. The material may not have a long-term purpose.
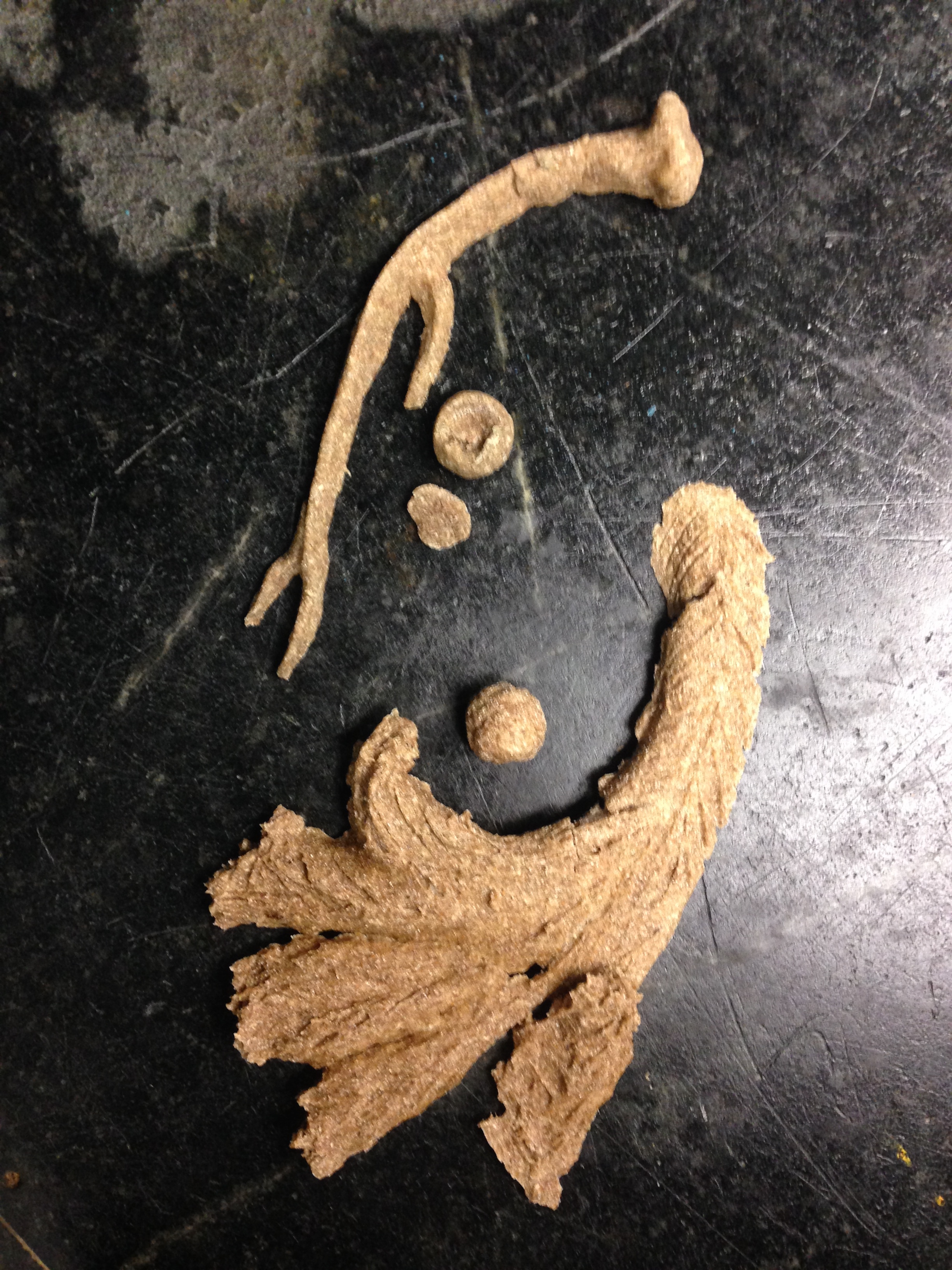
- Observations:
- Over coming the material: Tragacanth gum is an amazing material. When added with water it comes to life and has a mind of its own. As much as I wanted to manipulate it, it stuck to what it wanted to, formed the shapes in parameter that were determined by it. The manipulation was like a negotiation rather than fitting any vision I could come up for it.