Name: David McClure
Date and Time:
2015.12.9, 10:20am
Location: Chandler Laboratory
Subject: Madder dye boiling
10:15am- Removed both jars containing madder dye from hot water bath. Extremely strong and unpleasant odor when crock-pot lid is removed; I can only imagine what the dye itself smells like. Hopefully the fume hood will be able to keep the stench to a minimum. The dye seems a little more purple than before, but it could just be the light in my kitchen.
10:30am- Set up 2 hot plates in the fume hood so I can boil both samples at the same time. Using 250 ml beakers to boil the dye and veneers samples, since it's the closest size to the 6 oz. jars. Added any reserved dye from two weeks ago equally between the two beakers, but still not enough liquid to cover the veneers. I don't think I will bother flipping the veneers to boil both sides; if there is any color difference between the side of the veneer that was submerged in the boiling dye and the side that was not I will note this. Hot plate set to 1. Luckily you can't smell the dye in the fume hood!
Veneers w/ no pre-soaking
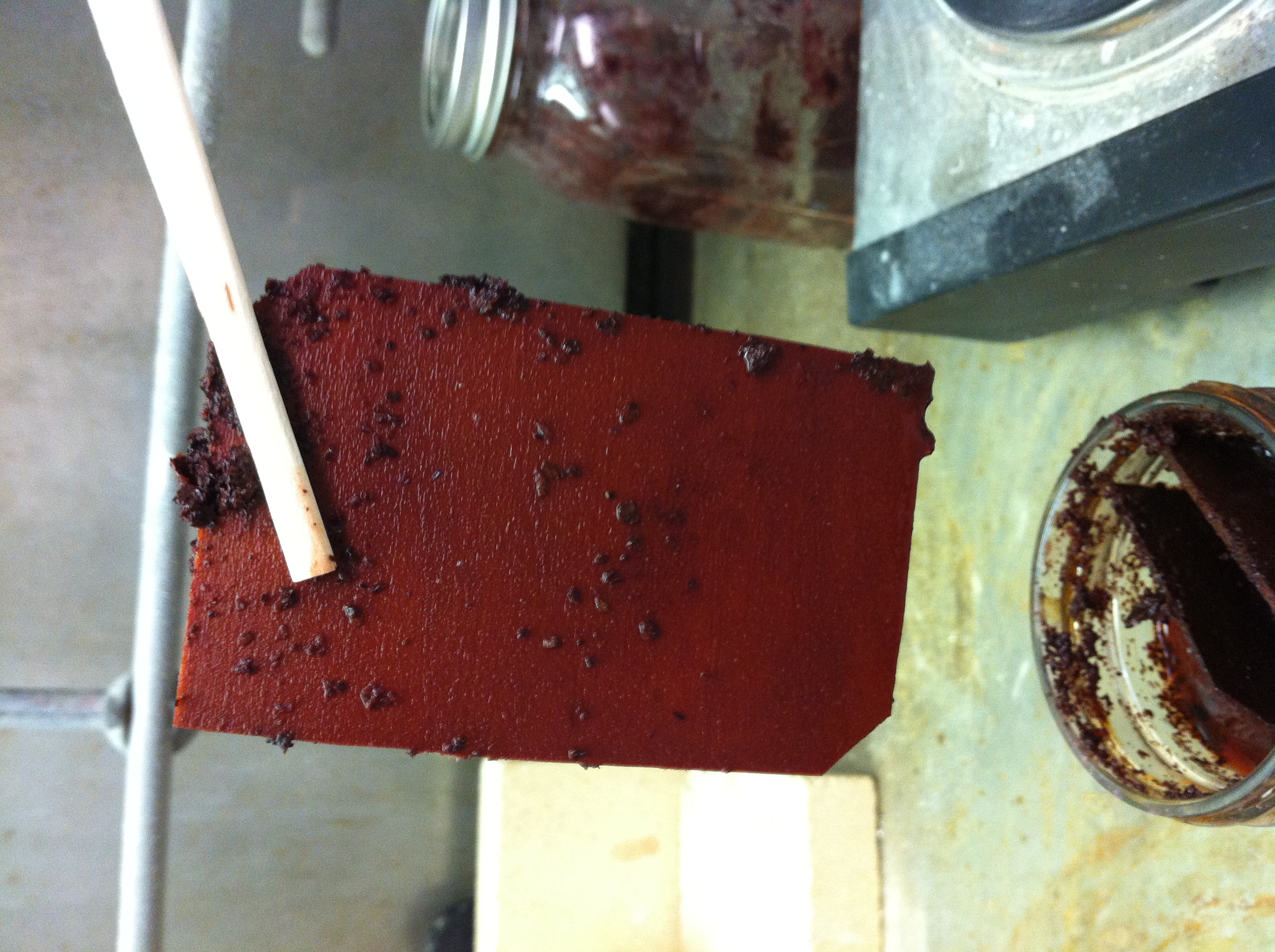
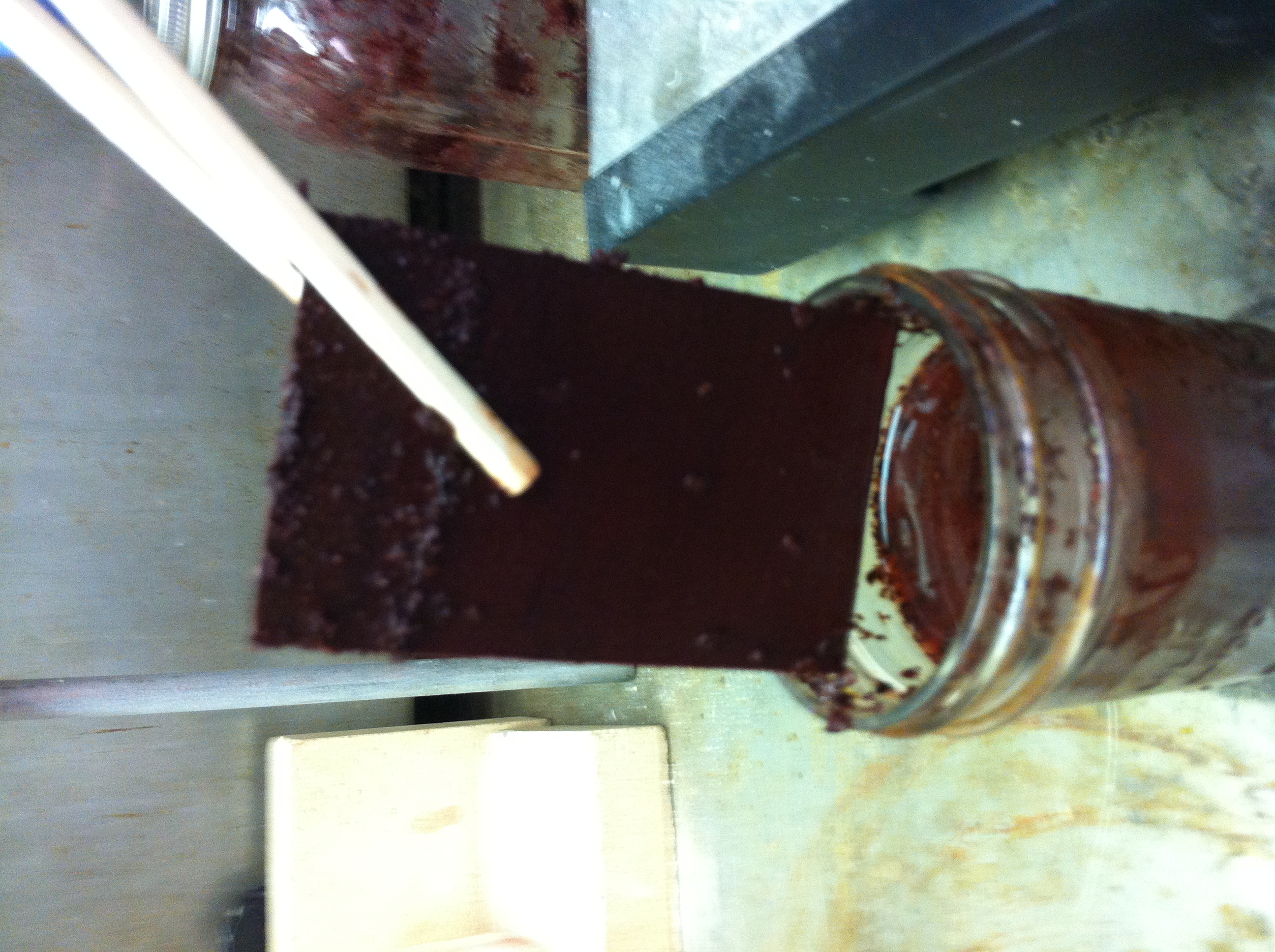
Pre-soaked veneers
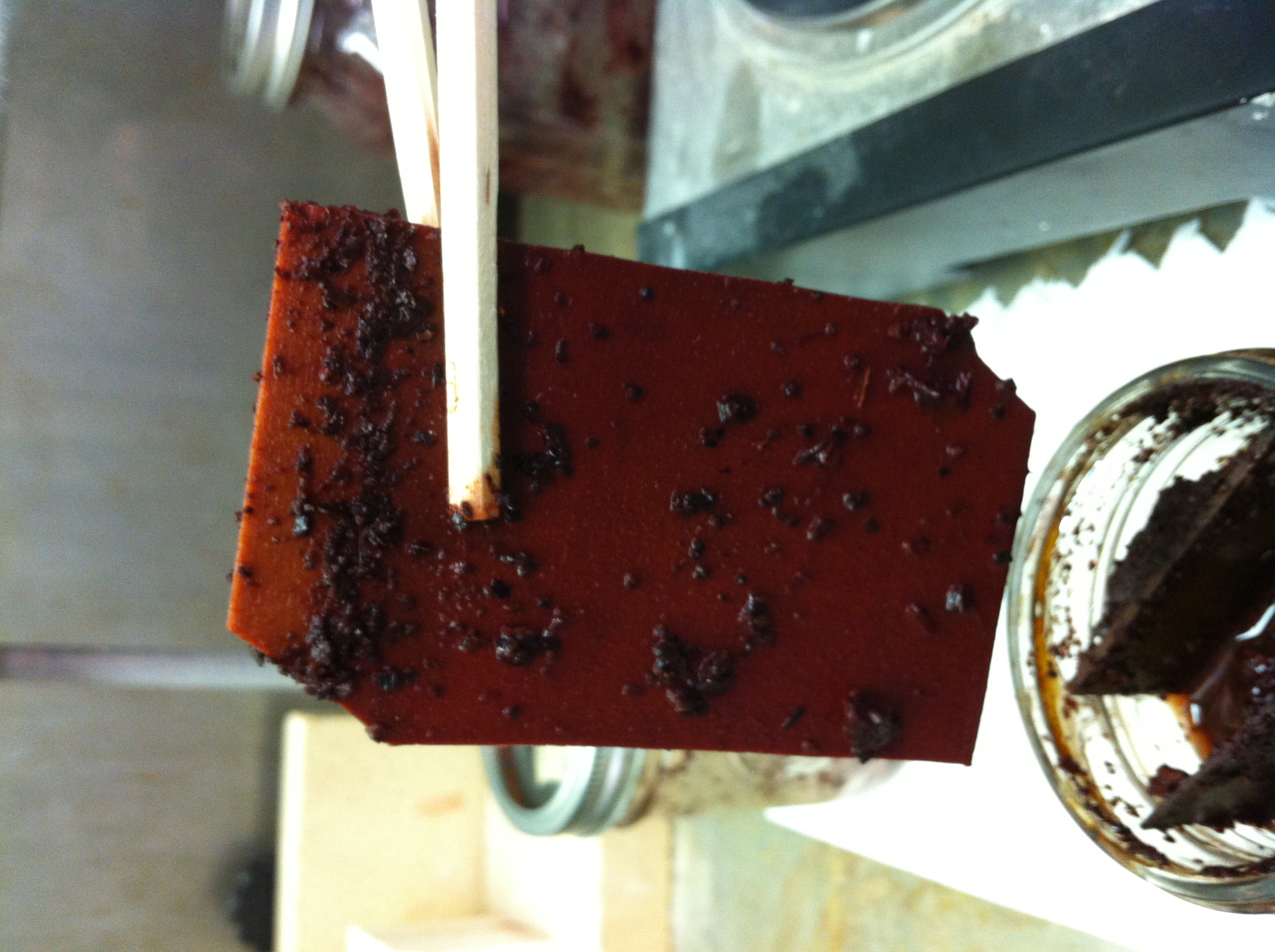
11:00am- Heat level of hot plate gradually increased to about 2.5, just starting a very light simmer. I want to keep it at this temperature because I'm afraid of boiling off all the liquid.
11:30am- Placed makeshift lids on top of beakers to try and slow loss of liquid during boiling.
11:40am- I'm having to constantly adjust the heat level of the hot plate because it seems to cycle on and off, sometimes raising the temperature substantially and bringing the dye to a vigorous boil.
12:30pm- Almost all of the liquid has been absorbed or evaporated, even though the heat is at the lowest setting needed to maintain a boil. I added 10 ml of water w/ a pipette to each beaker at Joel's suggestion to keep the madder grounds and veneer from drying out and burning.
1:10pm- Liquid again almost completely gone. Decided to just end experiment here. Removed veneers from beakers and set out to dry on paper towels in the fume hood. Pre-soaked veneers on top.
Name: David McClure
Date and Time:
2015.12.15, 12:00pm
Location: Chandler Laboratory
Subject: Madder dyed veneers - sanding, cutting, and final results
12:00pm- The veneers are certainly red. Trying to remove the particles of ground madder that stuck to the veneers while drying is hard; while our author practitioner gives no instructions about this, I'm guessing I should have strained the ground madder from the dye before boiling to avoid this problem. Maybe we didn't even need to keep the madder grounds in the jars during the 15 days soaking period? Can you find any other recipes that give specific instructions about this? Also the madder at the bottom of the beaker definitely got too hot and scorched the veneer, so the bottom of each sheet is slightly blackened. Lightly sanded one side on the wood with 1000 grit sandpaper; after the dust is brushed away the color seems more even and the grain a little more prominent than before.
12:10pm- With Donna's help used a jewler's saw to cut a small (about 1 mm) strip from the side of each veneer to see how deeply the dye penetrated the wood.
12:15pm- Wow. The dye barely penetrated AT ALL. It basically just stained the surface of the wood. There is also NO DISCERNIBLE DIFFERENCE between the samples that were pre-soaked in water and the veneers that were added without soaking. The color is the same, the depth of pigment penetration appears the same. Even though I was able to make red wood I'm not sure this experiment was particularly successful. I could easily sand past this surface layer of dye with medium-high grit sandpaper, which would seem to make these veneers pretty unsuitable for inlay work.
Cut veneers w/ no pre-soaking
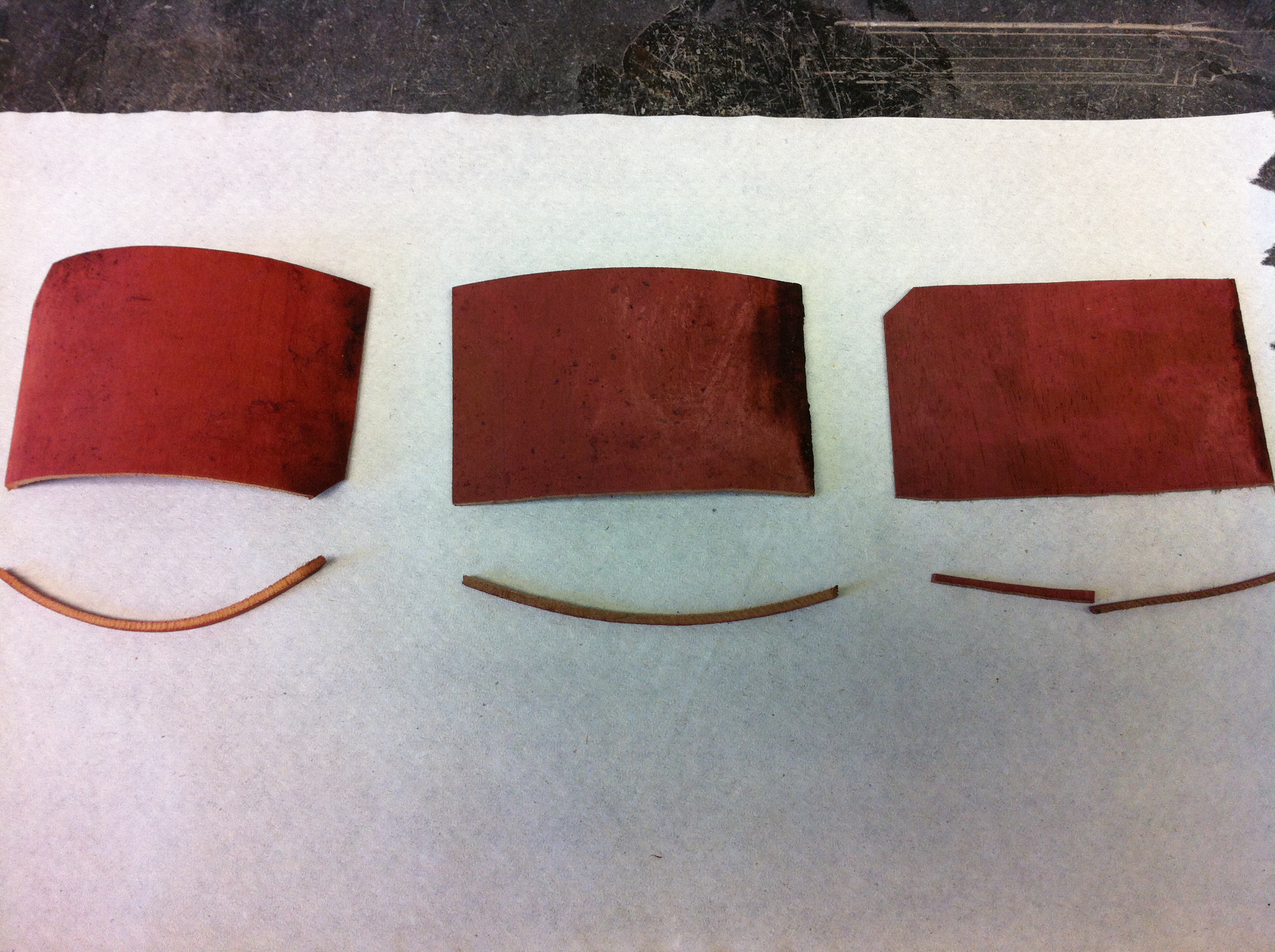
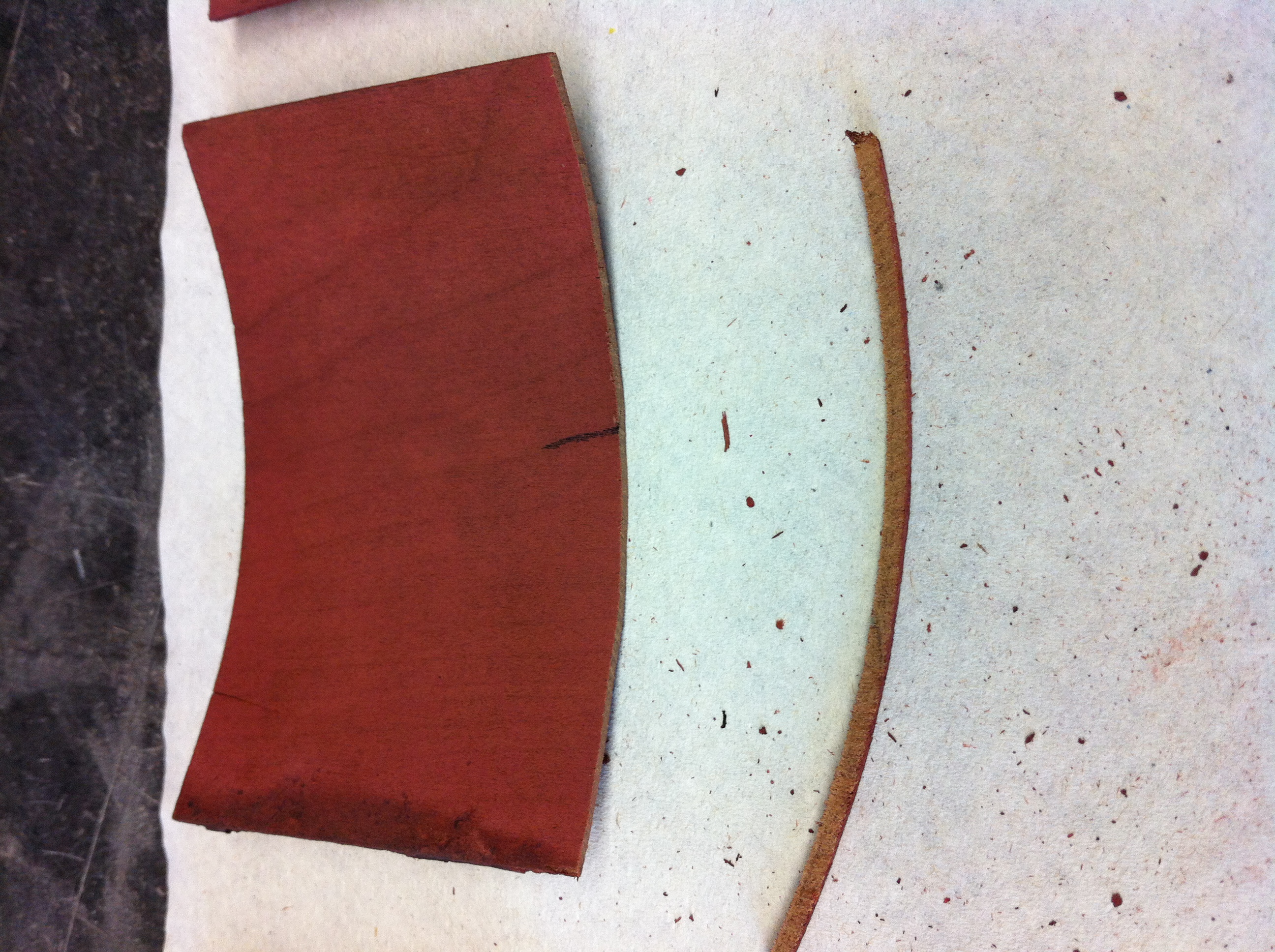
Cut pre-soaked veneers

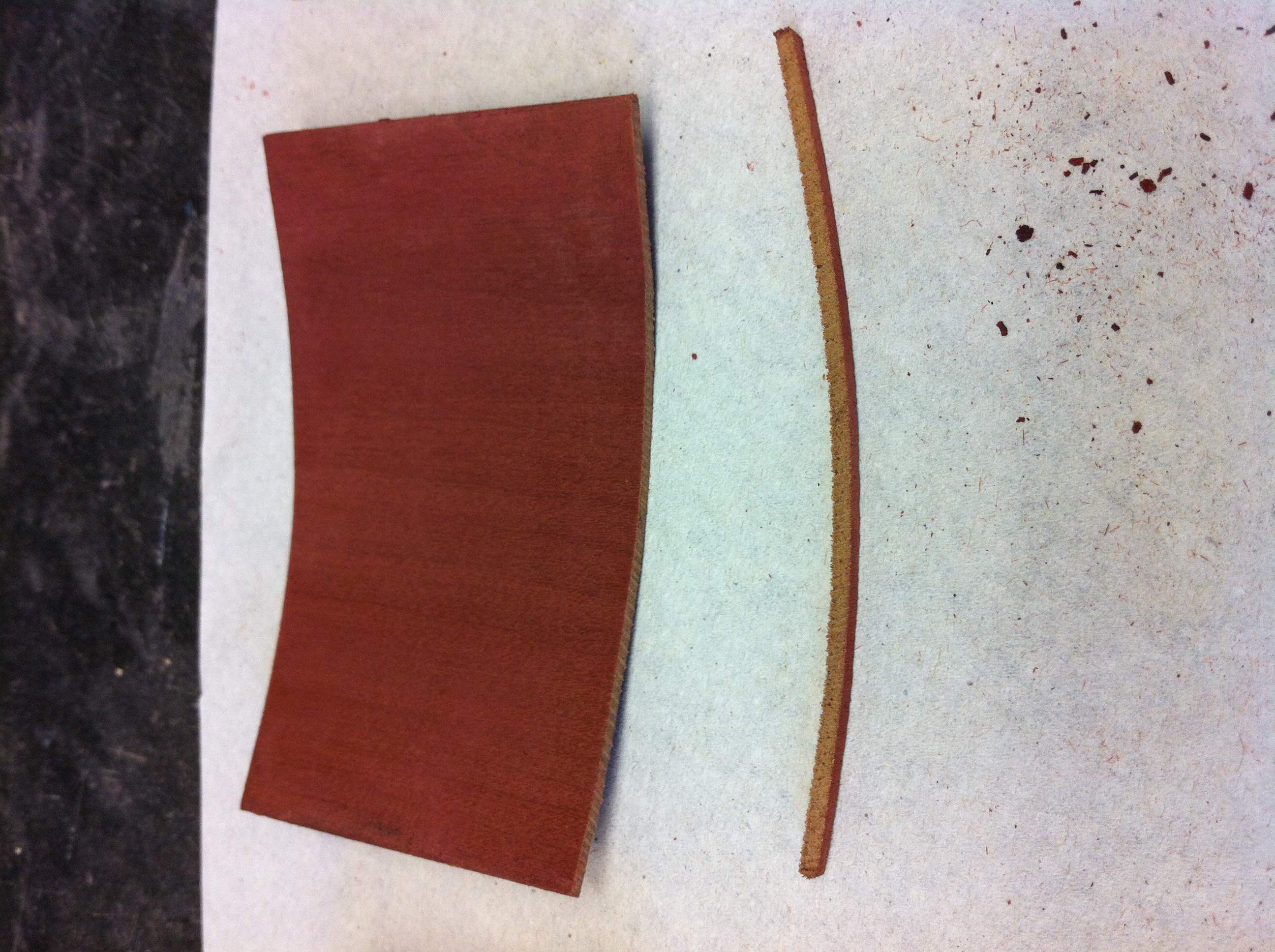
Final thoughts and possible ideas for future reconstructions
I'm fairly surprised by these results. I'm not sure I would describe this as a "dye," seeing as only the surface of the wood absorbed any color even though the wood was completely soaked through with the hot dye for 15 days. At first I was also surprised the pre-soaked and non-soaked samples were indistinguishable, but now I'm beginning to think the wood needed to be prepared in some kind of mordant solution like alum water (common in later wood dye recipes) instead of just tap water. If I had enough time and materials to do additional reconstructions I would have one sample group soak in a solution of alum and water for at least 48 hours but otherwise follow the same protocol as above, and another set prepared with vinegar instead of urine with 3 sample groups: non-soaked wood, wood pre-soaked in vinegar, and wood pre-soaked in alum water. I think it's likely the lack of an acidic liquid in this dye reconstruction also had something to do with the shallow penetration of the pigment, but I would need to do another reconstruction to be sure. If it is the case that an acidic liquid for the dye gives better results it raises even more questions about the use of urine in these recipes. So far Naomi and I have both failed to produce acidic dye through aging alone. Is this simply an issue of our diet? Do we just need to age the urine longer or in different circumstances (eg. in sunlight as opposed to in a dark cabinet)? It would also be interesting to see how if / how quickly the color begins to fade. According to Yannick Chastang even by the 18th century artificially dyed woods in inlay work faded "if not in weeks or months, then certainly within a few years," noting that a roll-top desk made by Jean-Henri Reisener and delivered to Versailles in 1769 required scraping to restore the original colors in 1776, 1777, and 1785 [Yannick Chastang,
Paintings in Wood: French Marquetry Furniture, p. 113, 115].
Veneers w/ no pre-soaking and original color
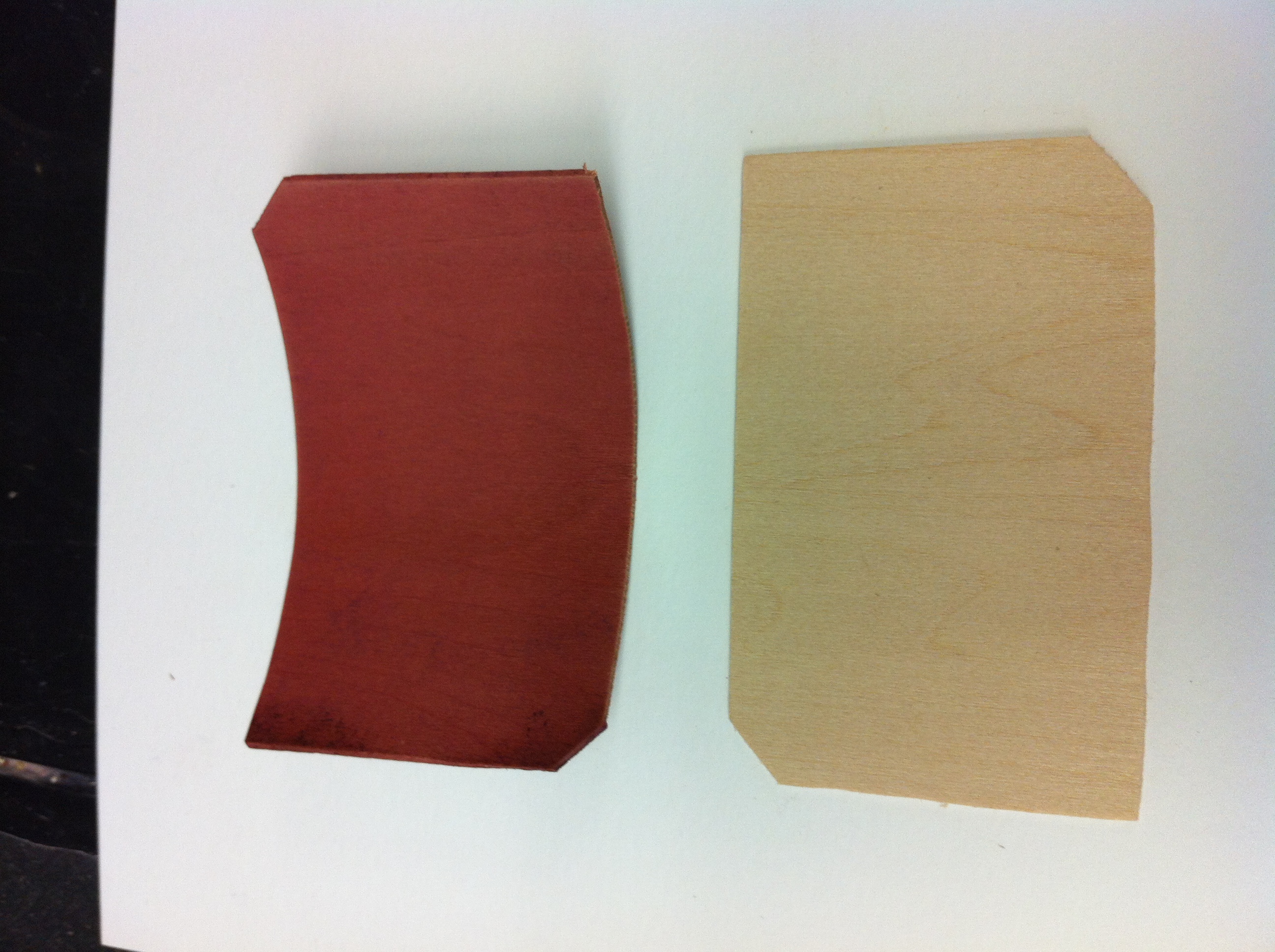
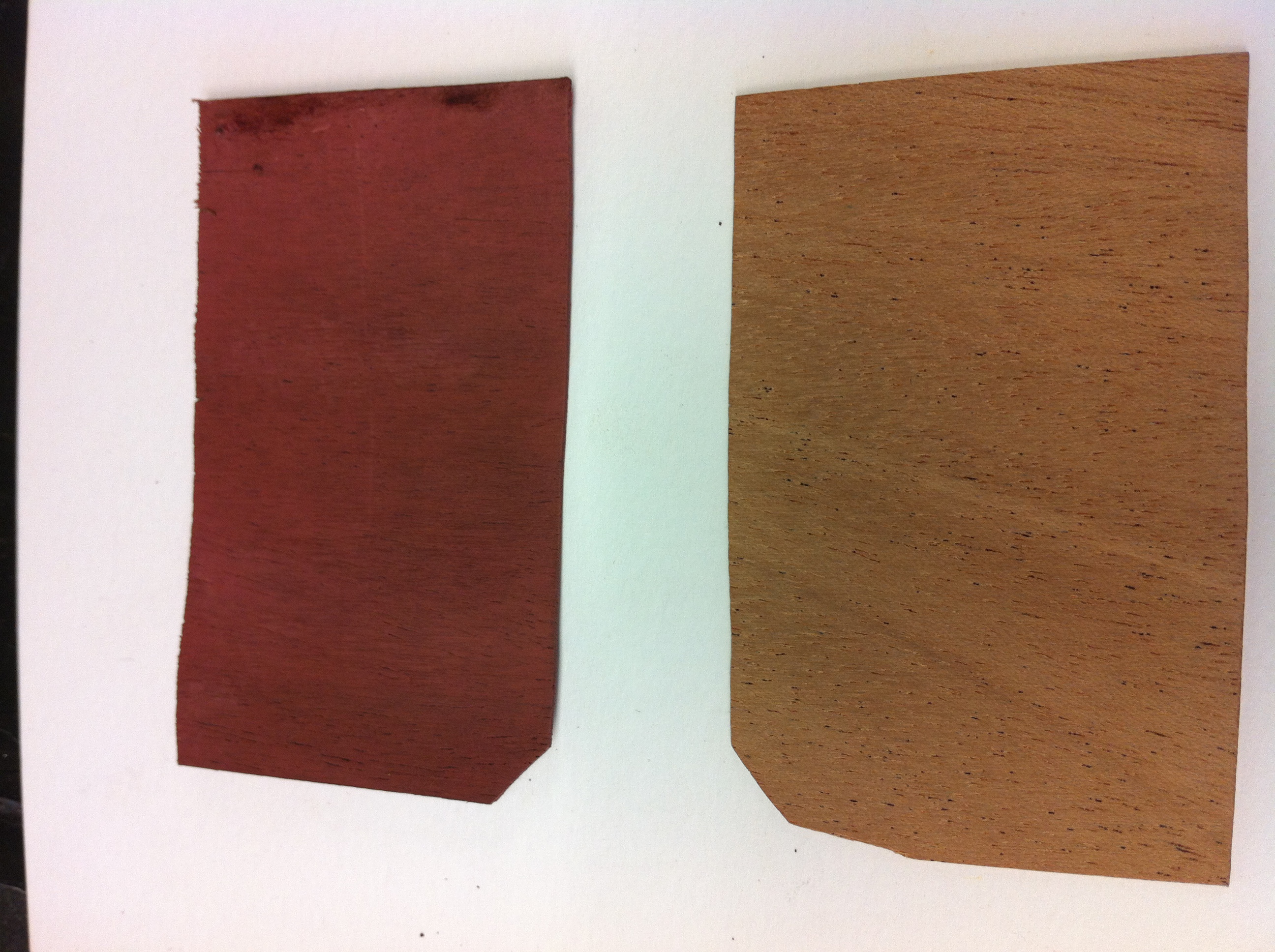
Pre-soaked veneers and original color
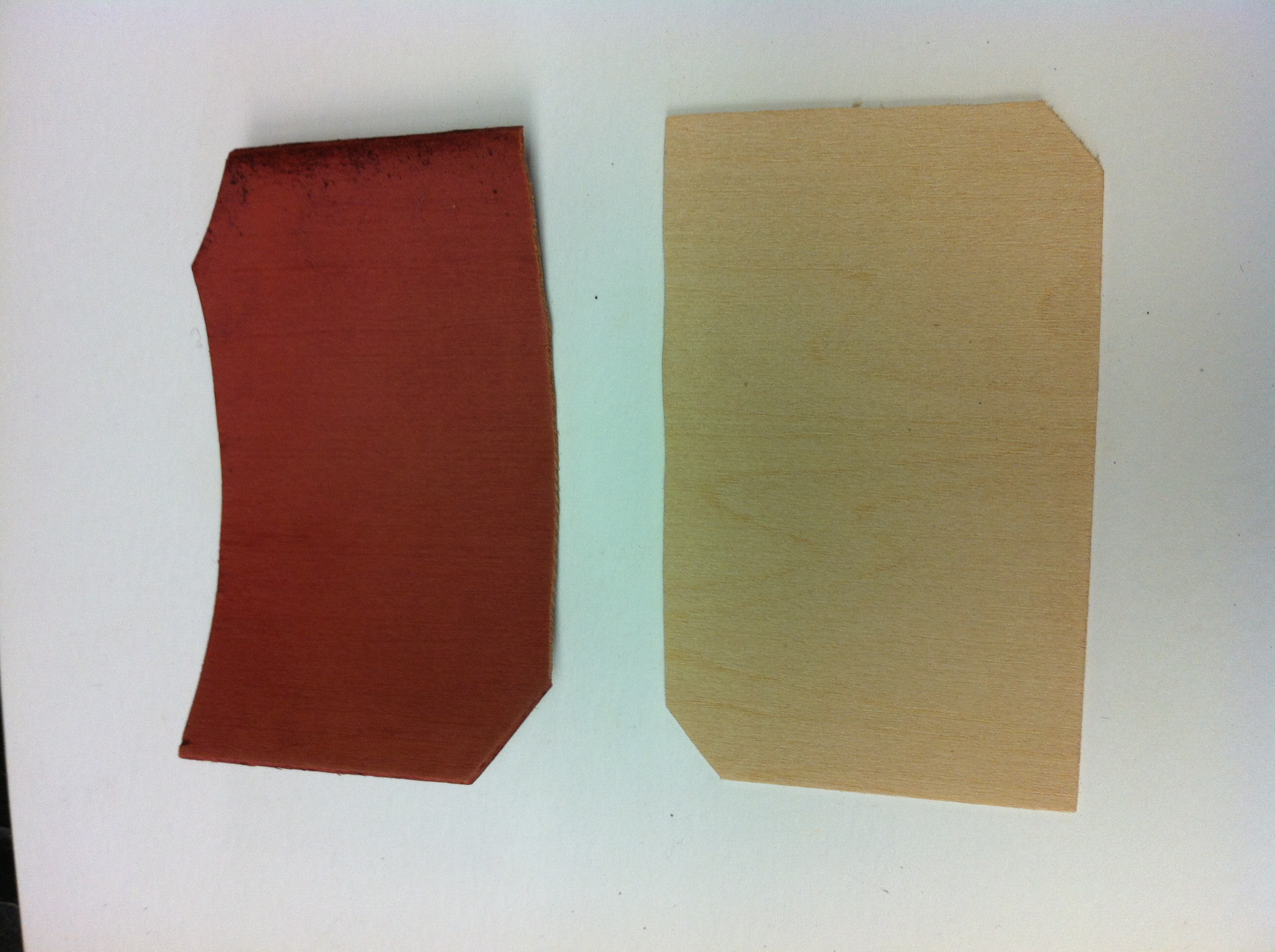
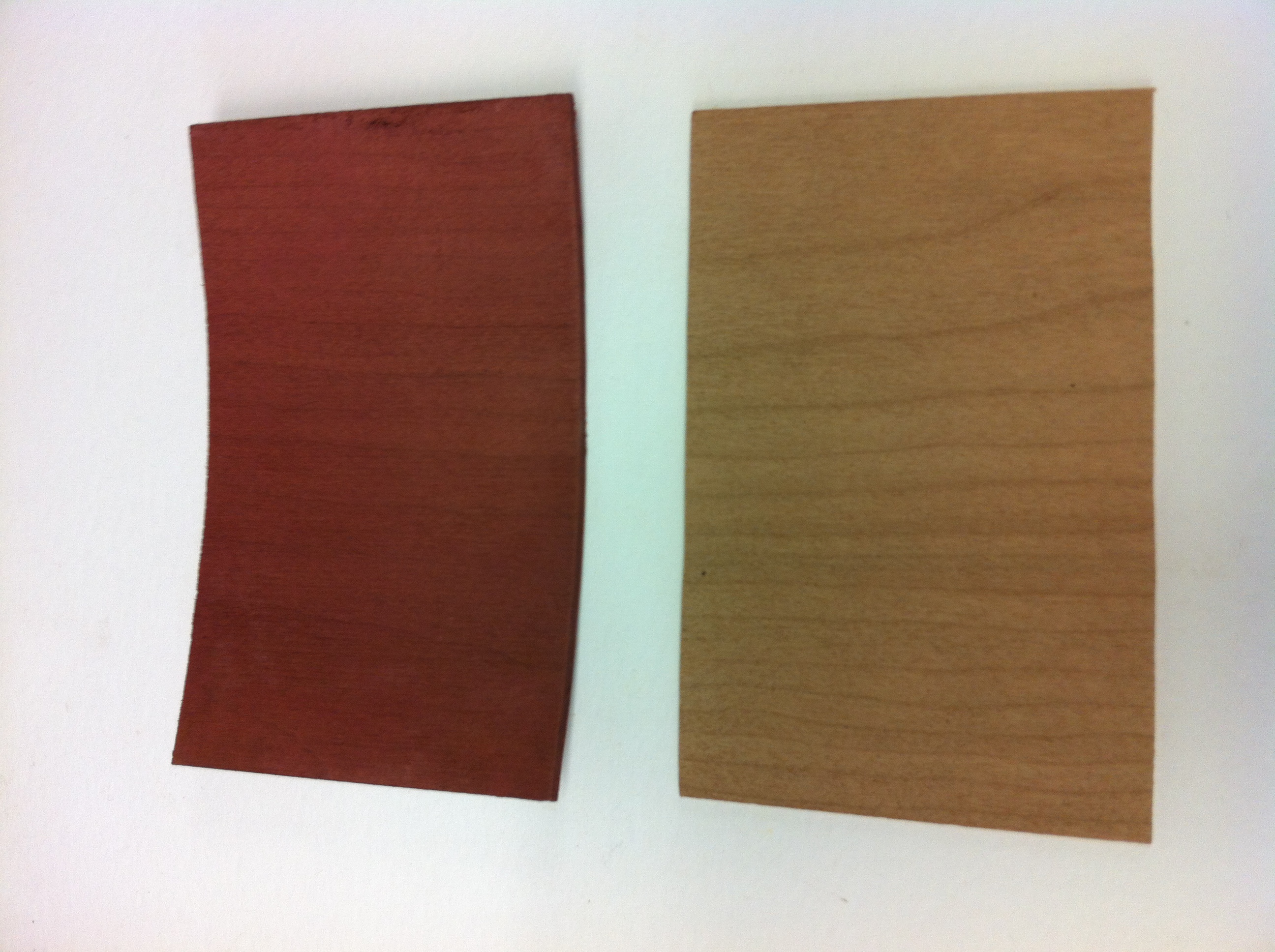